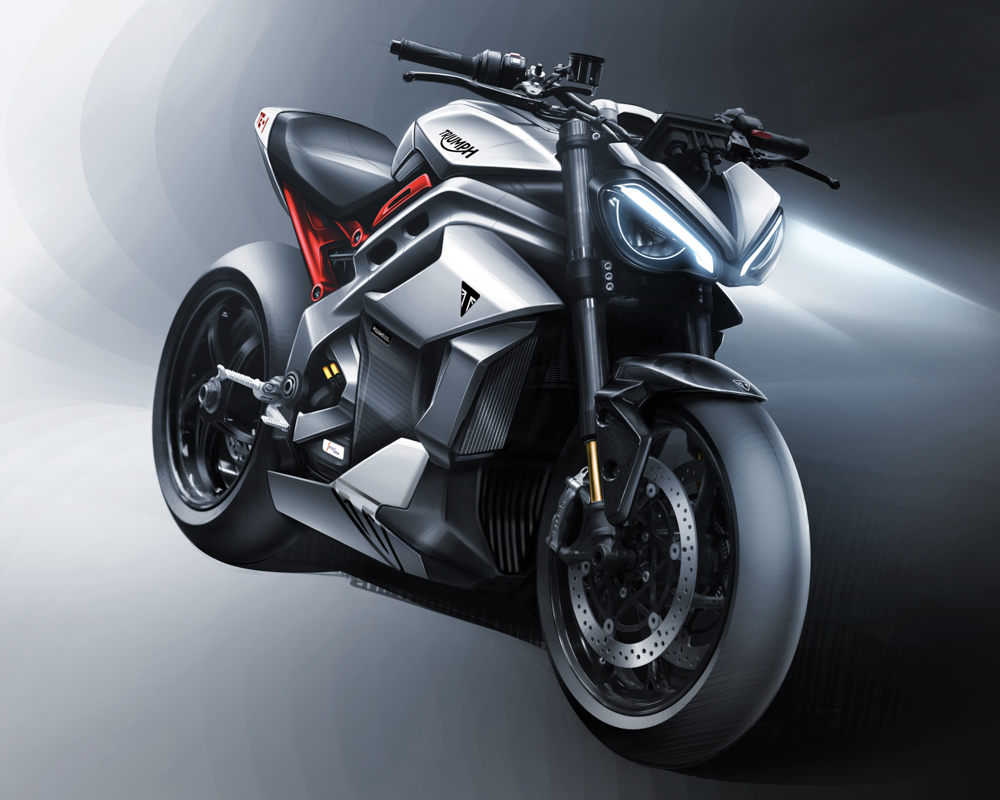
Triumph Motorcycles recently announced the completion of Phase 2 of the TE-1 electric motorcycle project, and the powertrain looks to have plenty of zoom. This research program was launched in May 2019 and is a uniquely British collaboration involving Triumph, Williams Advanced Engineering, Integral Powertrain, and WMG at the University of Warwick. Funding for the project is courtesy of the UK Office for Zero Emission Vehicles.
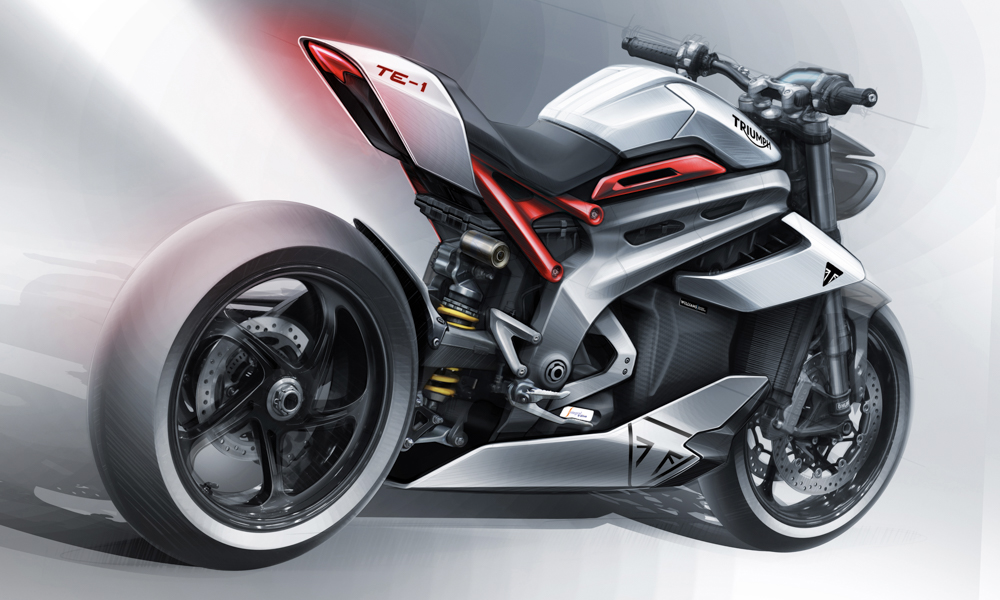
It’s well known that the challenge for electric vehicles is endurance and consistent power delivery. To achieve long range, you need to be very conservative with the “throttle.” As the battery loses its charge, it also begins to reduce power output. On the other hand, a conventional combustion engine can deliver 100% power until it runs out of fuel.
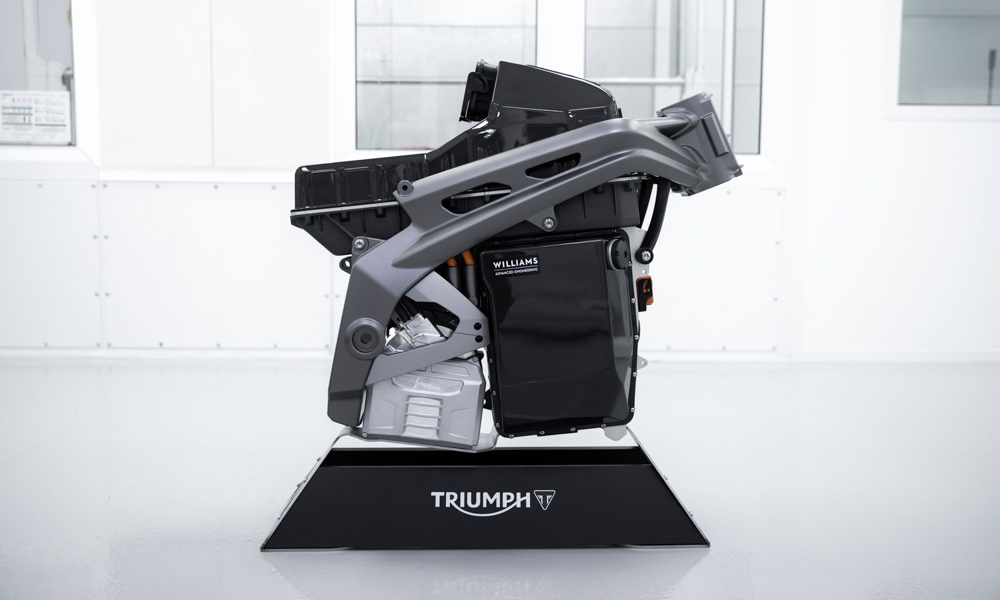
To get around this challenge, the TE-1 engineers focused on developing a compact drivetrain and the use of silicon-carbide technology. For Phase 1, they reduced the mass and volume of the power unit by integrating the motor and the inverter into a single component. By eliminating the mounting features, additional boxes, coolant pipework, and heavy high-voltage connections usually required by separate units, the propulsion system is lighter and more compact.
For Phase 2, the team turned to silicon-carbide technology instead of traditional transistor-based parts in the inverter to reduce energy losses and increase the drivetrain efficiency, the power delivery and the range. The prototype motor has been tested to produce 174hp while weighing just 10kg.
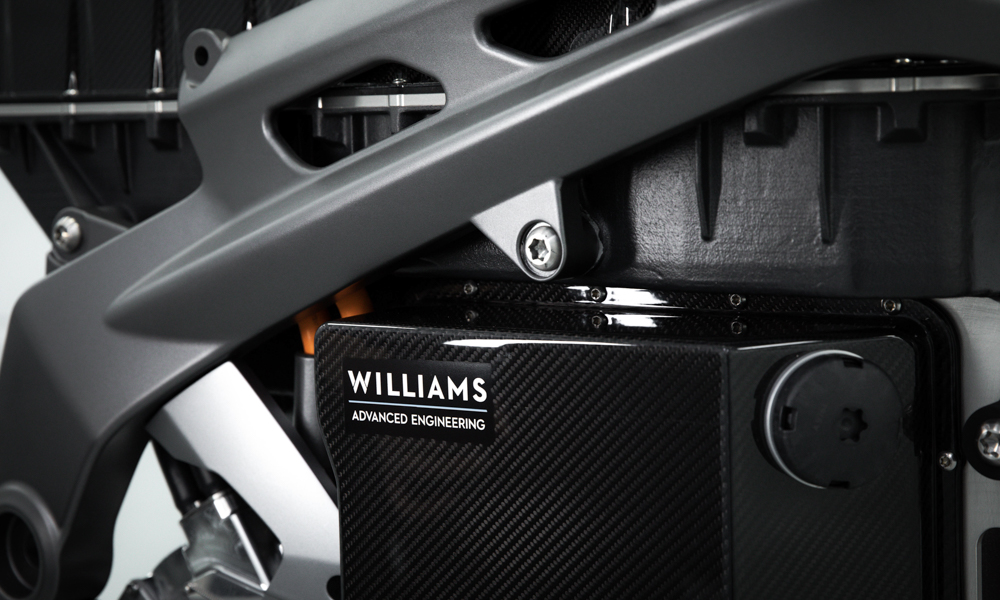
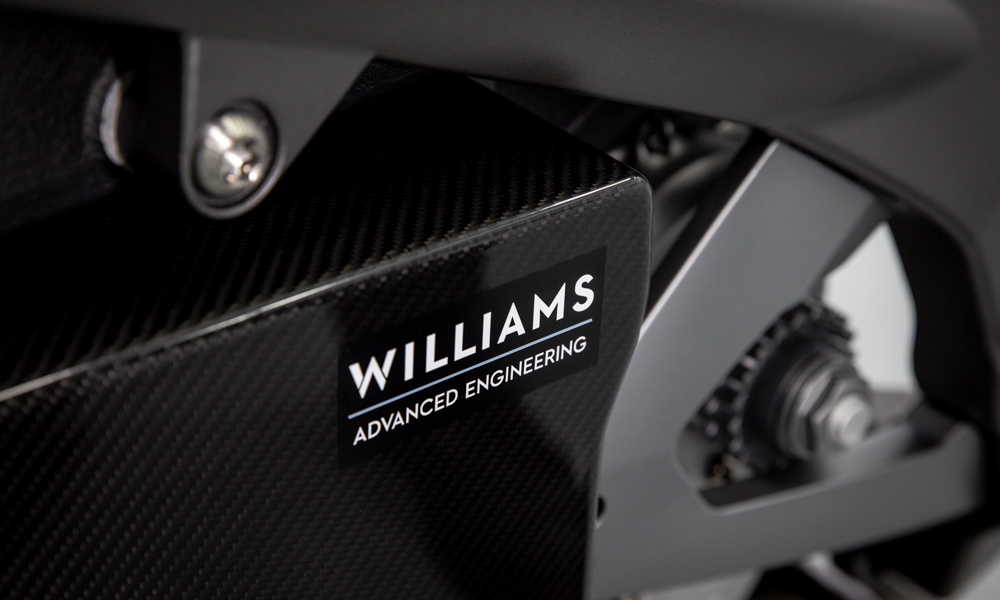
Next, the engineering team turned to Williams Advanced Engineering for the battery. Drawing on their experience in Formula E, the engineers optimized the battery module layout to balance mass and positioning within the chassis. A new vehicle control unit is integrated into the battery pack to minimize weight and packaging, while battery management software was developed to ensure consistent power delivery.
“Within the current landscape, most electric motorcycle technology arguably delivers compromised performance at low levels of battery charge,” said Dyrr Ardash, senior commercial manager for Williams Advanced Engineering. “By using a lightweight, compact solution, we have been able to give the rider all of the performance all of the time (regardless of battery charge), and a class-leading range. We have focused on pushing the boundaries to reduce mass and optimize frame position to benefit handling. We have also pushed the limits of battery performance, balancing the design for acceleration and range, with simulations modeled on track-based riding. In other words, as aggressive as possible.”

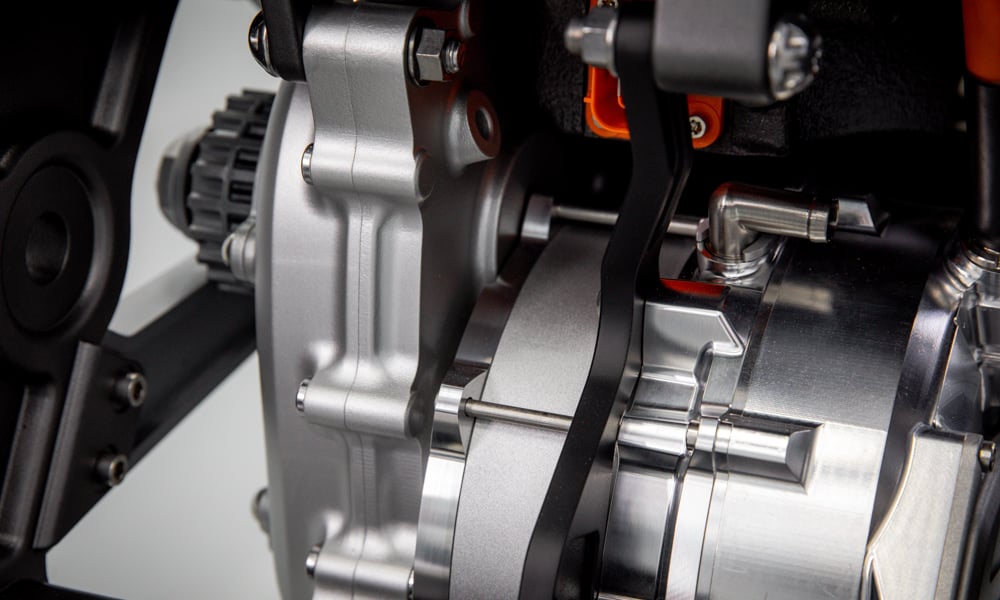
For its part, Triumph has been developing an all-new vehicle control software that incorporates all the electrical systems for throttle response, regenerative braking, traction control, and other rider aids. An advanced chassis including the main and rear frames is being worked on to fully maximize the space efficiency of the battery and the motor for Phase 3, and then mule testing by Phase 4.
For now, Triumph has released a series of renderings that give a strong hint of what the final prototype will be. Even though the concept drawings have the silhouette and the “angry fly” look that is reminiscent of the Speed Triple minus an exhaust muffler, this doesn’t mean that the company will actually mass-produce just such an e-bike anytime soon.
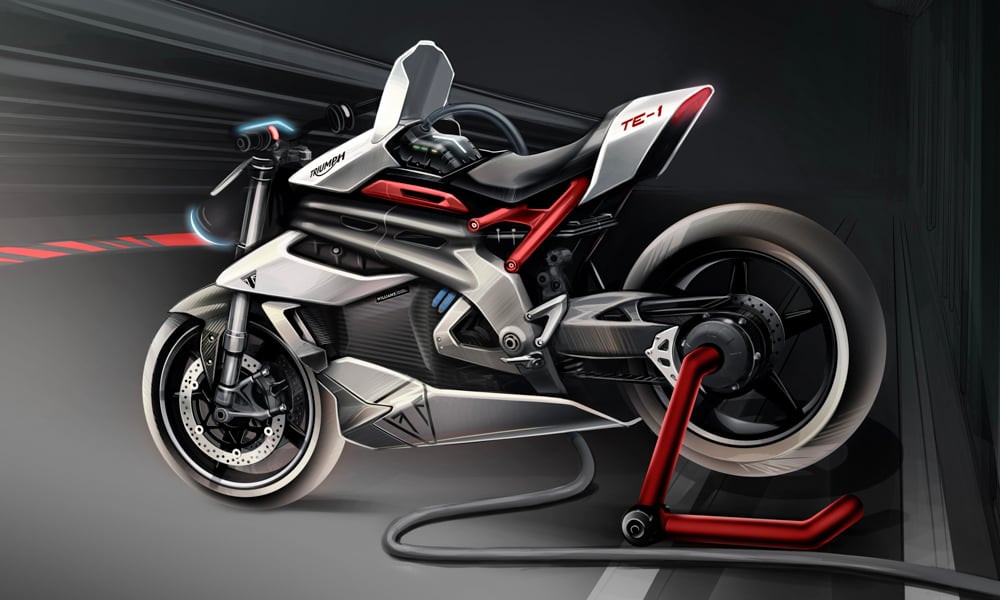
The TE-1 is a collaborative two-year project focused on the electrification of the UK’s motorcycle industry, but the knowledge derived from the project will influence Triumph’s long-term electric motorcycle strategy. With the technologies designed to be scalable, actual mass-produced e-bikes may generate less or more power depending on the intended model and target market.
0 Comments